Product Testing
Every home has dirty surfaces that need to be cleaned. Luckily, store shelves hold hundreds of different cleaning products, but how do consumers differentiate cleaning products? How do consumers balance performance, application, and value?
Cleaning product manufactures run tests in their labs to make sure their products perform. Testing comes in many forms, but the best tests replicate actual product use as close as possible. This is referred to as consumer relevant applications testing.
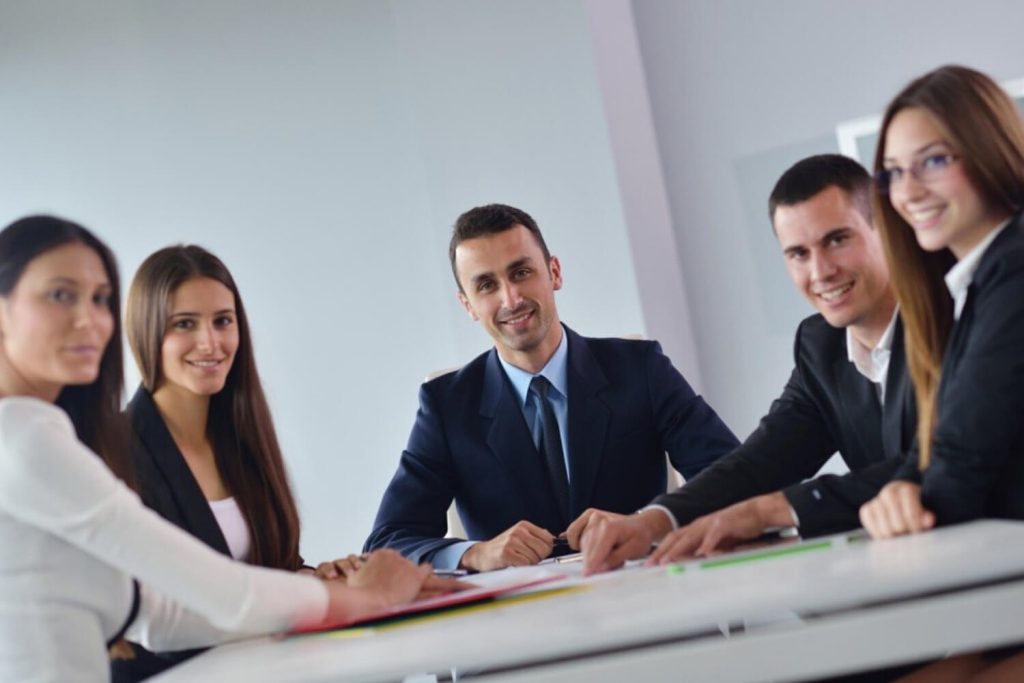
Consumer relevant applications tests begin by selecting a cleaning surface (the substrate) that represents common household places like kitchens, garages, or bathrooms. Next, a soil that mimics dirt found in these areas is selected or created. This soil may consist of grease, oil, common dirt, or even lab made soap scum. To get the most realistic soil, cleaning manufacturers then bake the soil onto the surface using an oven at various temperatures. This increases soil adhesion, so the soil does not wash off with water providing much clearer detail on how well the cleaner cleans.
For hard surface cleaners, the soiled surface is secured in an apparatus (in-line scrub tester) that uses a sponge secured in a weighted metal holder, which replicates a person holding the sponge and applying pressure to clean. Cleaning solution is applied to the soiled surface and the sponge, which is wet with additional cleaning solution or plain water depending on the test. The apparatus moves the sponge across the soiled surface a specific number of times, removed from the machine and rinsed with water. Surfaces are then examined by comparative test panels or by lab instrument to determine how much soil was removed. The former provides a comparative qualitative opinion on how well the test cleaning solution cleans, the latter provides a quantitative value of the % soil removed based on how much light reflects back to the instrument from the cleaned surface. In either case, the results can be used to compare to other products or a standard representing the desired level of clean.
This is just one example of how cleaning products are tested. As indicated by the number of cleaning products on the store shelves, however, each cleaning product has its own specific test that determines whether the product is a premium performer or a value brand. The HCPA compendium provides complete test methods for a full range of cleaners, soils, and surfaces.
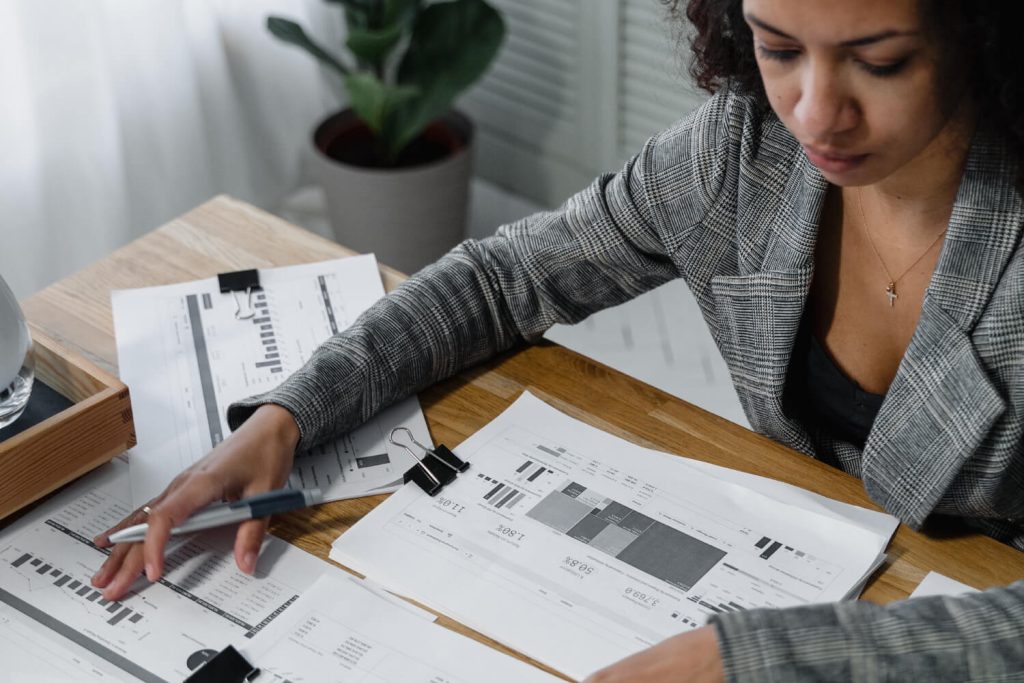
Enzyme Science
The enzymes used in cleaning formulations are all bacterial in origin. The enzyme companies have huge bio-reactors (often called fermenters) where they grow bacteria that produce the desired enzyme(s). Fermentation starts with a vial of dried or frozen microorganisms called a production strain. The production strain is selected to produce large amounts of the enzyme(s) of interest. Through multiple fermentation steps, where the microorganisms are kept at optimal pH, temperature, and nutrient conditions, so the desired amount of enzyme is produced. When the main fermentation is complete, the mixture of cells, nutrients, and enzymes, referred to as the broth, is ready for filtration and purification.
The recovery step follows fermentation. The recovery process typically consists of a pretreatment followed by a primary separation of the enzyme from the biomass. Afterwards, the enzyme is concentrated by removal of water and then unwanted impurities are removed in a purification step. Following recovery is a formulation or standardization step. Although much effort focuses on finding the right enzyme molecules for a given application, formulation plays a big role in the final use and success of the enzyme product. A new enzyme molecule with excellent performance can fail in the market if the enzyme is not stable during transportation and storage. The right formulation can remove these shortcomings and the importance of having the right formulation cannot be underestimated.
As stated in the introductory enzyme page, all enzymes are proteins. As such enzymes are capable of triggering allergic reactions in some people. Enzymes can also act as sensitizers. To avoid these problems enzymes are typically provided as dust free granulates or as liquid solutions. Granulated enzymes are produced using a unique combination of high-shear granulation and various coating technologies. This results in an effective encapsulation of the enzyme, which isolates it from the environment until the moment the detergent product is dissolved into the washing solution. In addition to ensuring optimal stability of the enzyme while being stored within the detergent, the granulate form also prevents undesired exposure. Liquid enzyme products are easier to handle but must be stabilized by incorporating polyols, sugars and/or salts. In the case of both granulated and liquid enzyme products, the enzyme must be capable of withstanding the detergent matrix for at least the target shelf life of the detergent without significant loss of performance.
Selecting the proper enzyme product depends not only the intended use conditions, but also on the type of enzyme needed. As stated in the introductory enzyme page there are three main types of enzymes used in cleaning applications, protease, lipase, and amylase. Additionally, there are many subcategories of each major class of enzyme and each subcategory performs optimally under slightly different conditions. As such the enzyme suppliers typically blend several different enzymes to make an enzyme product, thereby ensuring acceptable performance under the wide variety of use conditions encountered. There are also several other classes of enzyme which are used in cleaning formulations to a lesser degree.
Proteases accelerate the breakdown of proteins into peptides and soluble amino acids. Proteases are basic ingredients in many cleaning products and are used worldwide because of their effectiveness on common stain components, such as food, grass, and blood. Some proteases have an affinity for specific protein soils; thus, the target stain will determine which protease should be added to a detergent formulation.
Amylases accelerate the breakdown of starch-based stains from foods such as such as cereals, gravy, potato and pasta dishes. Amylases promote complete removal of starch at low wash temperatures. Starch is a long-chained carbohydrate consisting of glucose molecules bound together by alpha-1,4-glycosidic bonds. During wash, certain amylases catalyze the hydrolysis of alpha-1,4- bonds in starch, leading to the decomposition of starch into soluble dextrins and oligosaccharides. Unlike starch, dextrins and oligosaccharides are readily soluble in water and are therefore easier to remove from the surface.
Lipases accelerate the breakdown of triacyl glycerols (lipids) into fatty acids and glycerol. Lipases promote the removal of body stains, animal fats, and vegetable oils from fabric surfaces. Fatty material trapped inside cotton fibers can give rise to visible discoloration on fabrics and these visible spots cannot be removed effectively at medium-to-low washing temperatures without use of a lipase enzyme.
Cellulases are used specifically in laundry detergents to improve the appearance of washed fabric. Repeated washing and wearing damages cotton fibers, resulting in areas with bristly cellulose microfibrils (“fuzz”) that eventually form pills. These microfibrils trap particulate soil, preventing white fabrics from staying white and making colored fabrics look dull. Cellulases cleave microfibrils and pills thereby releasing any trapped particulate soil and helping maintain the brightness of colors on cotton fibers. Cellulases also aid primary stain removal by modifying the surface of cellulosic fibers and fabrics, making it easier for stains to be removed.
Mannanases break down mannans, an adhesive material found in guar gum and locust bean gum. Mannans or galactomannans are polysaccharides consisting of a mannose backbone linked together by β-1,4-linkages with side-chains of galactose attached to the backbone by α-1,6 linkages. Mannanases cleave the β-1,4-linkages of mannans, thus breaking down the gum polymer into smaller, more water-soluble carbohydrate fragments that can be easily removed from the surface being cleaned.
Pectinases degrade pectin, a complex polysaccharides that contains 1,4-linked α-D-galactosyl uronic acid residues contained in the primary cell walls of terrestrial plants. Pectinases catalyze the eliminative cleavage of (1-4)-α-D-galacturonan to give oligosaccharides with 4-deoxy-α-D-galact-4-enuronosyl groups at their non-reducing ends. This means that pectinases cleave the pectin into smaller, more water-soluble fragments that can easily be removed from the surface being cleaned. Pectinases provide unique stain removal benefits on a wide range of pectin-based stains from fresh fruits such as tomatoes, oranges, bananas, and berries, and from various processed foods containing extracted pectin such as tomato sauces, jams, jellies, and low-fat dairy products.
Enzymes are a sustainable solution to many cleaning problems. A relatively small amount of enzyme can have a significant impact on the overall cleaning performance of a detergent formulation. Moreover, enzymes require relatively mild conditions for optimal performance, thus the use of moderate pH conditions and cooler temperatures is favored. Years of testing has proven that enzymes have a very safe toxicological profile. Enzymes are not mutagenic and not clastogenic. They are not reproductive or developmental toxins and have a low toxicity to aquatic systems.
Microbiological Science
A biological product is a formulation that includes one or more beneficial living microorganisms and is used for a wide variety of environmentally beneficial tasks such as waste treatment, cleaning, and odor control.
Microorganisms (such as bacteria or fungi) are naturally occurring, ubiquitous (found everywhere), and necessary for our environment to function. While there are several pathogenic bacteria that present a public health risk (e.g. MRSA, E. coli, Salmonella, etc.), there are many others that are beneficial and necessary for survival. There are various species of bacteria in and on our bodies, like those that aid in digestion producing vitamins to keep us healthy. This example is the very definition of a symbiotic relationship – beneficial microorganisms thrive off the organics our bodies produce as waste by-products and, in return, the microorganism digestive process provides vital vitamins and nutrients to keep all of us healthy and happy.
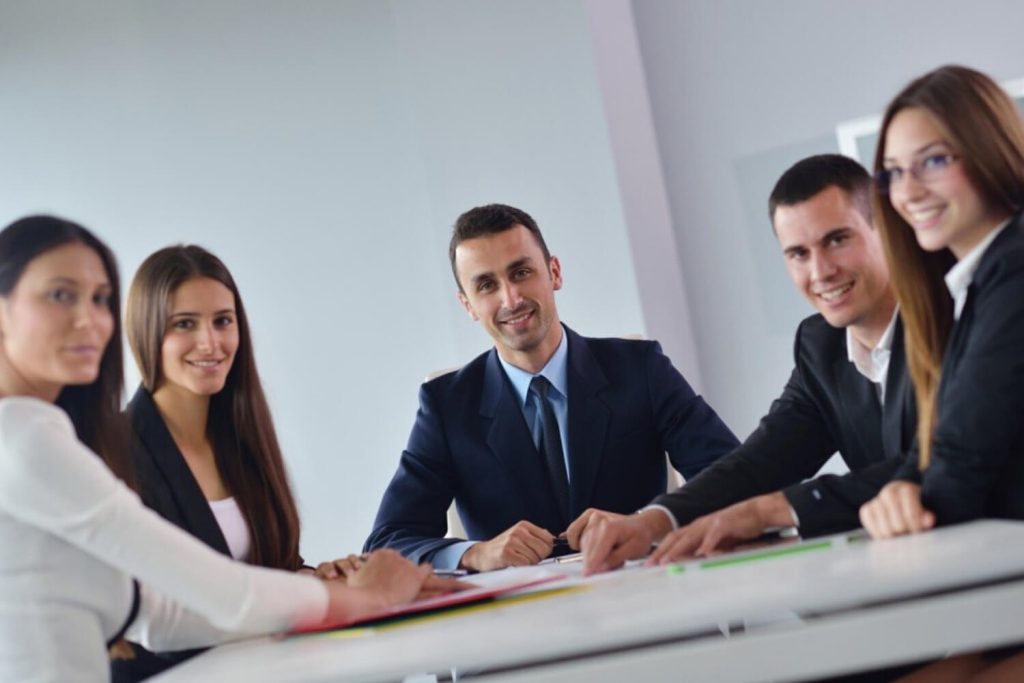
Beyond our own bodies, beneficial microorganisms are also hard at work maintaining the critical cycles of life in nature. They break down organic materials (e.g. compost pile), help plants grow and thrive, and some even degrade toxic chemicals. As we have come to understand the great power of, scientists have discovered ways to harness the performance of these beneficial microorganisms to do things like ferment wine, break down man-made waste, and enhance the effectiveness of cleaning and odor control products.
In the cleaning process, microorganisms work continually over time, resulting in longer term effects. Other formulated product components, like surfactants and solvents, that work quickly (1-2 minutes) can be combined with microorganisms to give longer and deep cleaning benefits only detectable after days and weeks of repeated use. Selection of all formulation components must be made carefully though, since not all are compatible with microorganisms. Biological products should only contain microorganisms that are safe for humans, animals, and the environment.
Benefits of using biological cleaning products include:
- Better stain removal
- Waste degradation
- Odor control
- Deep cleaning
- Grease removal
- Drain and grease trap maintenance
- Septic system maintenance
- Increased fabric whiteness
Biological products are an effective and sustainable option for a wide variety of applications and are safe for consumers and the environment.
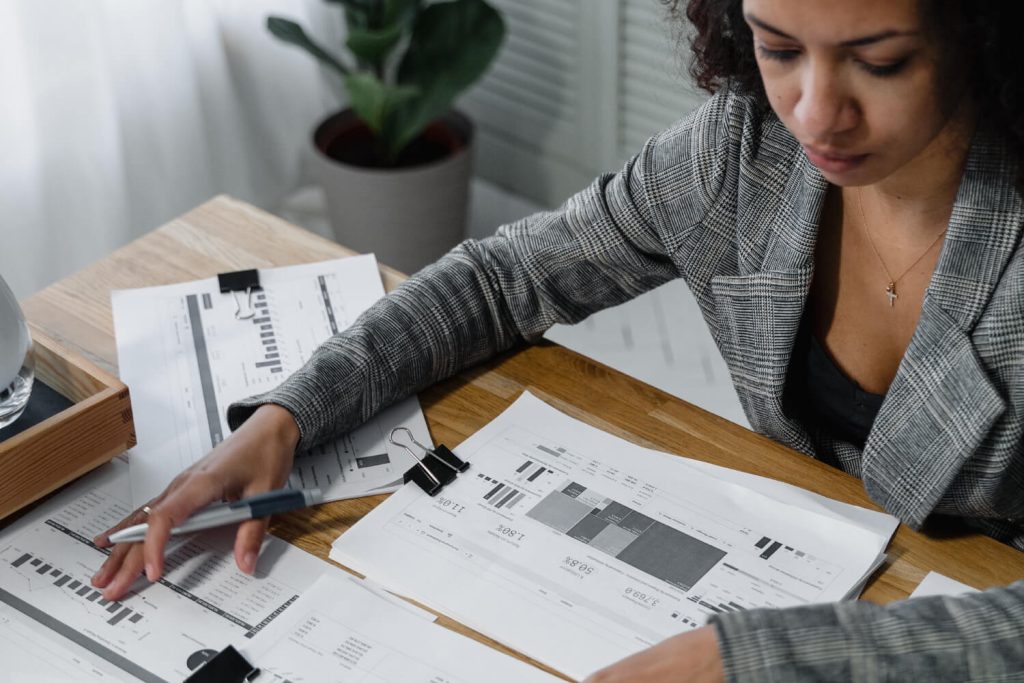
Solvent Science
A solvent is a material that dissolves another material, the solute, to form a solution. In a solution, the individual molecules of the solute are uniformly distributed among the molecules of the solvent, in contrast to a dispersion or emulsion where much larger particles of a material are dispersed in another material. Solvents and solutions are usually thought of as liquids, although solid solutions such as dye in the beeswax of colored candles, gaseous solutions such as our atmosphere, or gas in liquid solutions such as carbonated beverages, are all around us.
The golden rule of solubility is that like dissolves like. In other words, polar solvents dissolve polar materials and non-polar solvents dissolve non-polar materials. Polarity results from a separation of charge, so hydrocarbon solvents like hexane are non-polar because the electrons in a carbon-carbon or carbon-hydrogen bond are almost equally shared between the two atoms. In contrast, for a carbon-oxygen or hydrogen-oxygen bond, the oxygen pulls the electrons closer to itself, making the oxygen more negative and the carbon or hydrogen more positive, creating polarity. Polar solvents typically contain oxygen, nitrogen, sulfur, or chlorine atoms. Structures of many types of common solvents are shown below.
Water is the most common solvent and is sometimes referred to as the universal solvent because many materials are known to dissolve in water to some degree. However, many organic or oily type materials have little or no solubility in water. For that reason, polar organic solvents are added to water-based cleaning formulations to help with removal of oily soils. By far the most widely used polar solvents are the oxygenated solvents such as alcohols, glycol ethers, esters, ethers, and ketones.
Polar organic solvents are used in water-based cleaning because of their dual ability to dissolve in water and penetrate oily soil deposits. While short chain alcohols and glycol ethers are polar compared to hydrocarbon solvents, they are far less polar than water. It is this intermediate polarity that makes these materials so useful in cleaning applications. The solvents are polar enough to be completely miscible with the bulk of the water-based cleaning product, yet also non-polar enough to be able to penetrate oily soil deposits. These solvents naturally partition between the soil and the bulk cleaning solution according to the relative solubility and relative volume of these two phases. Given that the volume of cleaning solution is large relative to the volume of soil and only the solvent penetrating the soil acts on the soil, relatively high concentrations of solvent are necessary to provide the desired cleaning benefit. Despite this drawback, solvents are commonly used for their ability to penetrate and swell oily soils and reduce their viscosity. This allows them to effectively wet the surface and break apart soil deposits exposing more surface area on the soil and increasing the efficiency with which the other components of the cleaning solution can act on the oily soil.
Solvents are also included in cleaning products for reasons other than soil removal. Specifically, solvents are often used for their ability to couple together components of a cleaning product which might otherwise be insufficiently soluble to remain in solution. The incorporation of solvents in products of this type prevents the product from becoming hazy and ultimately separating into two layers. Solvents are also used for their ability to modify the viscosity of a cleaning product, making an otherwise very viscous formulation pourable. Finally, solvents are used to enhance the evaporation rate of cleaning products from a surface that has been cleaned. The most common example of this type of use for solvents is glass cleaners, almost all of which contain one or more organic solvents.
Surfactant Science
All surfactants have molecular structures that include both hydrophilic (water-loving) and hydrophobic (water-hating) parts. It is this feature which imparts surface activity to surfactants. When added to water, the hydrophilic parts are easily dissolved in the water, whereas the hydrophobic parts are water insoluble. This results in the surfactant orienting itself at the interface between the water and the vessel holding the water, as well as the surface between the water and the air. In each case the hydrophilic part of the surfactant oriented towards the water and the hydrophobic part of the surfactant oriented away from the water.
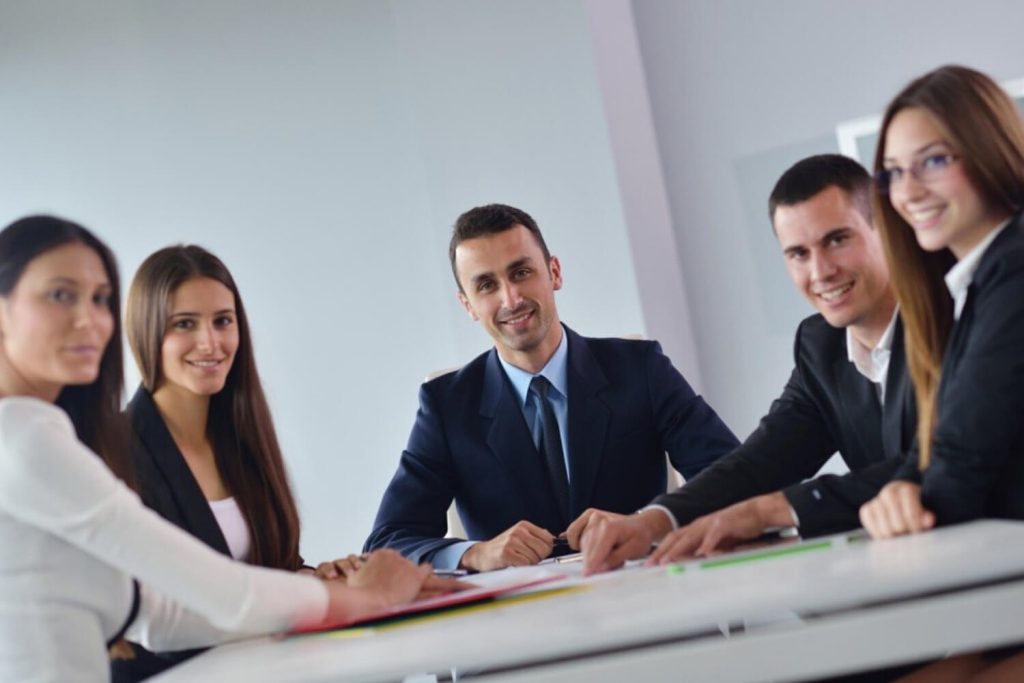
Consider a drop of water on a freshly waxed surface. The surface is very hydrophobic and water cannot easily wet or spread over the surface. The water tends to associate with itself rather than the waxy surface, forming a bead on the waxy surface. If surfactant is added to the drop of water, the surfactant would migrate to the surface of the water drop, where the hydrophobic part of the surfactant molecule can easily associate with the waxy surface. Thus, the surface tension is lowered and the water bead begins to spread and wet out more of the waxy surface.
This ability to reduce surface tension is a key measure of surfactant performance. The amount by which surface tension may be reduced is dependent upon several factors including the amount of surfactant which can exist at the water surface, referred to as the packing density. When a low level of surfactant is added to water some of the surfactant will dissolve in the water and most will migrate to the water surface. As more and more surfactant is added to the mixture, the solution and the surfaces both become saturated. When this happens, additional added surfactant forms soluble aggregates with their hydrophilic parts oriented outward, toward the water, and their hydrophobic parts oriented inward, away from the water. These aggregates are called micelles. The concentration at which micelles start to form is called the critical micelle concentration or CMC. The surface tension for a given surfactant is minimized at or above the CMC, meaning no more surfactant can be accommodated at the surface and, thus, no further reduction in surface tension will occur.
Surfactants work by attaching their hydrophobic portions to an oily soil on the surface. The surfactants then work between the oily soil and the surface, effectively increasing the available surface area for surfactant. This process, which ultimately removes the oily soil deposit from the surface, is known as oily soil roll up and is represented in the figure below. Individual surfactant molecules are represented by the pin shape, where the solid circle represents the hydrophilic head group and the straight line represents the hydrophobic tail group. The oily soil deposit is represented by the open circle.
Surfactants are commonly classified or grouped based on the electrical charge of their hydrophilic head groups. Accordingly, surfactants are classified as anionic (the head group contains a negative charge), cationic (the head group contains a positive charge), nonionic (the head group does not contain a charge), and amphoteric (the head group contains both negative and positive charges depending on the pH). The charge on a surfactant will give it specific properties and functionality.
Anionic surfactants, with an overall negative charge, account for the largest class of surfactants in terms of volume surfactant used. Widely used anionic surfactants include sulfonates, sulfates, ether sulfates and carboxylates. Anionic surfactants are the major surfactant in most hard surface cleaners, including manual dish wash products, all-purpose cleaners, floor cleaners, bathroom tub and tile cleaners, and a whole range of specialty hard surface cleaners. In general, anionic surfactants are high foaming products, although there are exceptions.
Cationic surfactants, especially those with longer hydrophobic tails, tend to be very substantive on surfaces. Because most surfaces carry a negative charge, the positively charged cationic surfactants have a high attraction to the negatively charged surface. Accordingly, these surfactants are used as hair and fabric conditioners adding softness or shine to these surfaces when attached. Cationic surfactants, with shorter hydrophobic tails, often demonstrate biocidal properties and are used as the active ingredient in many disinfectant and sanitizer products.
Nonionic surfactants include alcohol alkoxylates, alkylphenol ethoxylates, ethylene oxide propylene oxide block co-polymers, fatty acid amides, fatty acid esters, and alkyl glucosides. In general, nonionic surfactants are good degreasers and create medium to low foaming products. Nonionic surfactants can be used in various applications where high foam is not desirable or in automatic dishwashing where foam is a detriment to good cleaning. They can be used in combination with any other surfactant types (both cationic and anionic), since nonionic surfactants do not have a charge to react with the charge of another surfactant type. Combining surfactant types can result in increased cleaning performance.
Amphoteric surfactants, often called zwitterionic surfactants, tend to form stable foam and, as such, are often included as a co-surfactant in products where a stable foam is desired. A amphoteric substance can be anionic or cationic depending on the pH. Under acidic conditions, these becomes cationic and at alkaline pHs they become anionic in nature. At a neutral pH near 7, amphoteric surfactants are relatively mild towards skin, hence they commonly used in personal care products such as shampoos and body wash products. Commonly used amphoteric surfactants include betaines, amphoacetates, amphopropionates, and amine oxides.
While the nature of the polar head group is highly variable and determines many of the overall characteristics of the surfactant, it is the balance between the head group and the hydrophobic tail group that gives surfactants their surface activity. Hydrophobic tail groups fall into three broad categories: linear alkyl chains, aryl ring structures (often with linear alkyl chains attached), and propylene oxide oligimers. The larger the hydrophobic group, the less water soluble the surfactant and the higher the viscosity of the solution. The reduced water solubility leads to a lower critical micelle concentration and more efficient surface tension reduction.
Surfactant structures with short chain hydrophobes, for example xylene sulfonate and cumene sulfonate, have very little surfactant character. Despite this, these materials are very useful as aids in solubilizing surfactants with relatively poor water solubility. These materials are called hydrotropes.
For a more detailed discussion of surfactants, their structures and their properties we refer the interested reader to the Surfactant Science Series of text books published by Marcel Dekker Inc. This series of textbooks contains over 70 volumes discussing all aspects of surfactant science.
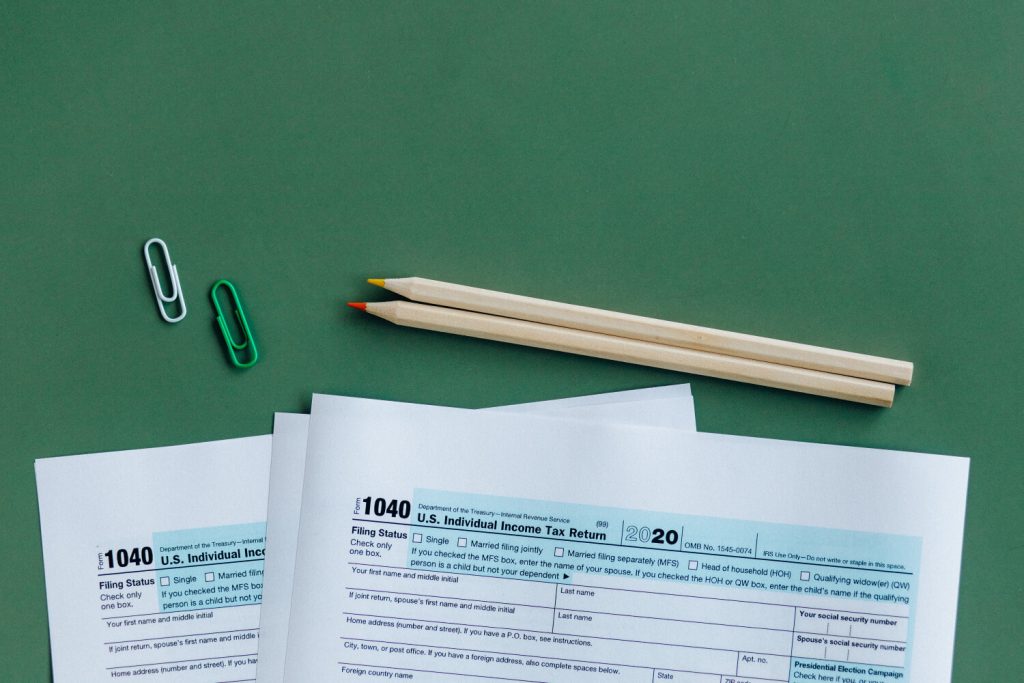
Chelant Science
A chelant, sometimes referred to as a sequestrant or a builder, is a specialized molecule designed to bind to positively charged metal ions, most commonly calcium and magnesium, in solution. This coupling prevents the metal ions from forming insoluble precipitates with other ions that may be present in solution. The two basic types of chelants are designated as hard and soft.
Hard chelants example EDTA (ethylenediamine tetra acetic acid) and NTA (Nitrilo triacetic acid) form very stable complexes with a 1:1 stoichiometry. That is to say that one EDTA molecule reacts with a single metal ion.
Soft chelants like polymers of acrylic and maleic acid form less stable complexes and function by preventing crystal growth rather than by true chelation.
Both calcium and magnesium ions form very stable insoluble precipitates with carbonate ion. Bicarbonate is ubiquitous in surface waters and is deprotonated by high pH cleaners to give carbonate. Insoluble precipitates are difficult to remove without the use of an acidic cleaner. These difficult to remove deposits are called hard water scale, and thus water containing calcium and magnesium ions is referred to as hard water. There are two common methods to deal with hard water. The first is to use softened water. Softened water has the calcium and magnesium ions removed. This is often accomplished by use of a water softener which exchanges sodium ions for the calcium and magnesium ions in solution. The second method is to use chelants in the cleaning product formulation. Chelating the calcium and magnesium ions in solution effectively prevents the formation of these deposits.
Calcium and magnesium ions also form insoluble precipitates with many anionic surfactants, most notably fatty acid carboxylates (soap). The formation of calcium soap complexes is so efficient that the concentration of free surfactant available for cleaning is reduced to effectively zero until all the calcium has been removed from solution either by chelation or by forming the insoluble soap adduct. Without the chelant present in a cleaning product more surfactant would be necessary to ensure that an effective concentration of free surfactant was available for cleaning. In other words, the consumer would have to use more of the cleaning product to obtain a desired result. Further, the insoluble calcium soap adduct would precipitate from solution onto the surface to be cleaned leading to a dingy appearance and a stiff feel on the washed fabric. Thus, chelants used for these purposes are sometimes referred to as “builders” as they help build upon the performance of the surfactant.
In addition to softening the water of the cleaning solution, chelants are also effective in helping to remove some stains, especially those that have a high metal ion concentration. Stains have a complex and varied molecular structure that often include metal ions cross linking and stabilizing the stain structure. Chelants present in the cleaning solution will bind with these various metal ions helping to remove them from the stain and thereby weakening the stain structure to facilitate its removal.
Beyond calcium and magnesium, chelants bind with all polyvalent metal ions in solution. Iron and manganese, although less prevalent, can also lead to significant cleaning problems including the formation of insoluble precipitates such as iron oxide, rust, and manganese dioxide. Therefore, specialty cleaners are often formulated with highly efficient iron chelators to bind with these ions, again eliminating the problems they might otherwise cause or helping to eliminate rust and iron stains that have already formed.
The table below shows many examples of chelating agents used in formulated products and their theoretical capacity to bind with or sequester calcium from water to improve cleaning performance:
Resources:
1. Synthetic Detergents Seventh Edition, AS Davidsohn & B Milwidsky, Longman Scientific & Technical, 1987
2. Akzo Nobel Dissolvine GL brochure, March 2004.
3. Dow Versenol 120 Chelating Technical Datasheet, June 2002.
4. Dow Versene HEIDA Chelating Agent Technical Datasheet. Form No. 113-01355-04-07.
5. Bayer Baypure CX-100 Edition 2001-11
6. ISP Unpublished data.
7. http://www.kelien.com/products/HEDP_2809-21-4.htm
8. BASF Trilon Types Chelating Agent, June 2008
9. United States Patent 3904685
10. JAOCS 60 (3): 618-622, March 1983
Bleach Science
Bleaching agents are materials that lighten or whiten a substrate (for example a fabric or hard surface) through a chemical reaction. They are used for textile, paper and pulp bleaching, laundry, and many other cleaning applications. Bleaching usually involves either oxidative or reductive reactions that decompose stains and soils. These processes may involve the removal or change of larger molecules and color-bearing groups in the stain or soil into smaller, more soluble units which are more easily removed in the cleaning process. The most common bleaching agents generally fall into three categories: halogen bleaches and their related compounds (such as sodium hypochlorite and sodium dichloroisocyanurate), oxygen bleaches (such as hydrogen peroxide and sodium percarbonate) and reducing bleaches.
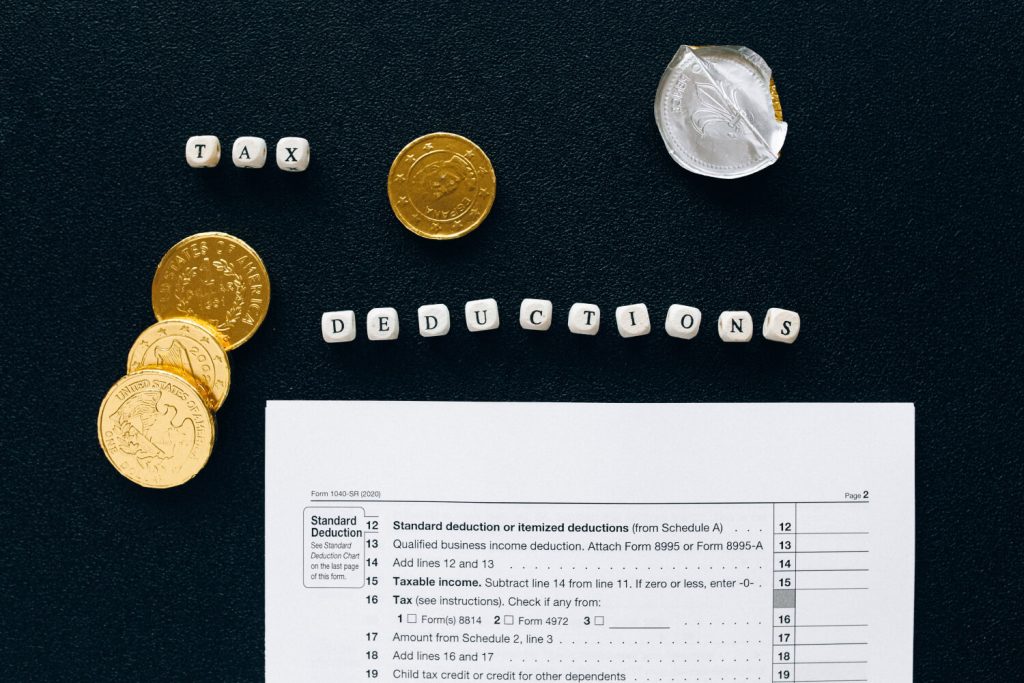
Halogen Bleaches
Halogen bleaching agents, mostly based on chlorine or bromine, are the most cost-effective bleaching agents. Besides being very effective at removing stains and soils, they are also highly effective antimicrobial products – indeed, water treatment is the largest use of chlorine‑containing bleaching agents.
The most common halogen bleaches may be divided into four classes: chlorine, hypochlorites, N‑chloro compounds, and chlorine dioxide. The first three classes are categorized as “available chlorine” compounds or “chlorine bleaches”, although hypochlorites and N-chloro compounds do not actually contain chlorine gas. They are related to chlorine by the equilibria in Equations 1-4, which occur very quickly in aqueous solution:
Cl2 (g) ⇌ Cl2 (aq) – (1)
Cl2 (aq) + H2O ⇌ HOCl + H+ + Cl – (2)
HOCl ⇌ H+ + OCl – (3)
RR’NCl + H2O ⇌ HOCl + RR’NH – (4)
Solutions of halogen bleaches decompose on standing, at a rate which depends on the solution’s composition and storage conditions. Hypochlorous acid and hypochlorite anions decompose according to Equations 5 and 6:
3 HOCl ⇌ HClO3 + 2 HCl – (5)
3 OCl ⇌ ClO3 + 2 Cl – (6)
Hypochlorite solutions are most stable above pH 11 where the rate of decomposition is nearly independent of pH. In this region, the rate of decomposition has a second-order dependence on the concentration of hypochlorite. Decomposition also increases with increasing ionic strength, thus concentrated solutions decompose much faster than dilute solutions. Further, because of an unusually high activation energy, the decomposition rate increases greatly with temperature. Nevertheless, solutions with less than about 7% sodium hypochlorite and a pH above 11 have acceptable long-term stability below about 30oC; if manufactured with best practices, consumers can expect hypochlorite bleach to contain at least the stated label strength by the time they purchase it and to retain at least half of its original strength after one year.
Decomposition also occurs by reaction 7:
2 OCl ⇌ O2 + 2 Cl – (7)
This reaction can usually be ignored unless the bleach is exposed to light (where ultraviolet radiation initiates the reaction) or unless it is catalyzed by transition metal ions. Even very small amounts of transition metal ions such as iron cause rapid decomposition. They form very reactive intermediates that can decrease the stability of oxidizable compounds in the bleach solution and increase the damage to substrates (e.g. appearance of yellowing, metal oxide deposits or, in extreme cases, degradation of fabrics).
The major form of hypochlorite produced is sodium hypochlorite, NaOCl. It is invariably made and used as an aqueous solution. It is usually prepared by the chlorination of sodium hydroxide solutions as shown in Equation 8, although other bases like sodium carbonate can be used as well.
Cl2 + 2 NaOH ⇌ NaOCl + NaCl + H2O – (8)
A 5 7% sodium hypochlorite solution is sold for household purposes, of which the largest use is in laundry. Solutions of 10 15% NaOCl are sold for swimming pool disinfection, institutional laundries, and industrial purposes such as cleaning of dairy equipment, restaurants, sanitizing industrial plant equipment and disinfecting cooling towers. Solutions of various strengths are used in household and industrial and institutional (I&I) cleaners, and disinfectants and sanitizers. A small amount is used in textile mills. Sodium hypochlorite is also made on site (to avoid rapid decomposition) for pulp bleaching.
Commercially important solid “available chlorine” bleaches (such as calcium hypochlorite and sodium dichloro¬iso¬cyanurate) are more stable than concentrated hypochlorite solutions. They decompose very slowly in sealed containers. However, most of them decompose quickly as they absorb moisture from air or from other ingredients in a formulation.
Oxygen Bleaches
Oxygen-based bleaches, also known as peroxygen bleaches, contain the peroxide linkage: ( O O ) in which one of the oxygen atoms is active. Hydrogen peroxide is one of the most common of these bleaching agents. It is the primary oxygen-based bleaching agent in the textile industry and it is also used in pulp and paper and home laundry appli¬cations as an alternative to sodium hypochlorite. In textile bleaching, hydrogen peroxide is the most common bleaching agent for protein fibers (e.g., wool, silk) and it is also used extensively for cellulosic fibers (e.g., cotton, rayon). Pure hydrogen peroxide has an active oxygen content of 47%. It is the least expensive source of active oxygen commercially available. Moreover, it is a liquid, making it convenient for many bleaching applications. It is a very weak acid and in aqueous solutions only dissociates slightly (Equation 9).
H2O2 ⇌ H+ + HO2 -(9)
Undissociated hydrogen peroxide is relatively stable, and for this reason most commercial products are adjusted to pH 4. Hydrogen peroxide is usually sold in solutions containing up to 50% of active material. Concentrated solutions of hydrogen peroxide are very hazardous and must be handled with extreme care: at concentrations above 5%, hydrogen peroxide can cause permanent eye damage. In concentrations of 15% and above, hydrogen peroxide is an aggressive oxidizer and is corrosive to many materials, including human skin.
Hydrogen peroxide bleaching is performed in alkaline solution where part of the hydrogen peroxide is converted to the perhydroxy anion (Equation 9). The perhydroxy anion HO2 is generally believed to be a key intermediate and its concentration in solution increases with hydrogen peroxide concentration, alkalinity, and temperature. The alkaline agents commonly used to generate HO2 are caustic soda orcarbonates. Better bleaching is obtained at these alkaline conditions by increasing the temperature or adding a bleach activator such as tetraacetylethylenediamine (TAED).
Hydrogen peroxide reacts with many compounds, such as borates, carbonates, pyrophosphates, sulfates, silicates, and with a variety of organic carboxylic acids, esters, and anhydrides to give peroxy compounds or peroxyhydrates. A number of these compounds are stable solids that readily hydrolyze to give hydrogen peroxide in solution, the most important being sodium perborate and sodium percarbonate. Solid oxygen bleaches, as in the case of halogen bleaches, are preferred for stability and compatibility with other sensitive ingredients. Another solid oxygen bleach, persulfate (the peroxygen product of hydrogen peroxide and sulfuric acid) is a powerful oxidizing agent. A commercially available salt, potassium persulfate, is a white solid having a satisfactory shelf life and an active oxygen content of about 4.4%. It is a triple salt with the composition 2KHSO5•K2SO4•KHSO4.
Peracids are compounds containing the functional group -OOH derived from an organic or inorganic acid functionality. Typical structures include CH3C(O)OOH (PAA) derived from acetic acid and HOS(O)2OOH (peroxy¬mono¬sulfuric acid previously discussed) derived from sulfuric acid. The cold-water bleaching performance and phosphate reductions in detergent systems accounts for the emergent utilization of peroxygen bleaches in laundry.
Peracids can be introduced into the bleaching system by two methods. Peracids can be manufactured separately and delivered to the bleaching bath with the other components or as an adjunct. Peracids can also be formed in situ utilizing the perhydrolysis reaction shown in Equation 10 (where L denotes a leaving group). The two main peracid precursors used are tetraacetylethylenediamine (TAED), which generates peracetic acid in the wash and nonanoyloxybenzene sulfonate (NOBS), which produces pernonanoic acid when combined with hydrogen peroxide in the wash water.
R-C(O)-L + HO2 ⇌ R-C(O)OOH + L- – (10)
As bleaching agents, oxygen bleaches are much less effective than hypochlorite. However, they do have some advantages over halogen bleaching agents, such as less potential damage to textile fibers and dyes, and lack of a strong odor. Attempts have been made to increase the laundry bleaching power of hydrogen peroxide-based laundry bleaches by the addition of heavy metal catalysts. However, the effectiveness of these systems is controversial; an early attempt to incorporate a catalyst into a laundry detergent led to fabric damage and was consequently withdrawn. Though catalysts have not been incorporated into commercial products in the U.S., they have found use in automatic dishwashing detergents in Europe.
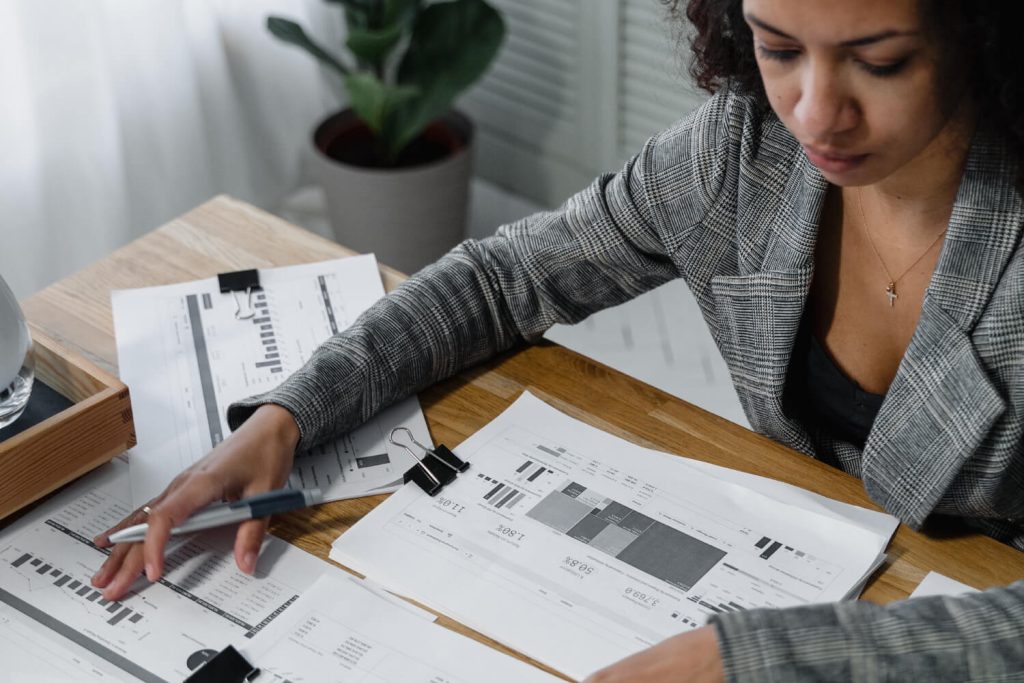
Preservative Science
Microbial contamination of cleaning products is highly undesirable for several reasons. Primary among these is the fact that we clean to remove contaminants from surfaces and, if the cleaning solution is microbially contaminated, we are in fact contaminating the surface rather than removing contaminants from the surface. This means that the surface is not clean, regardless of its physical appearance, and this can lead to contamination of materials that may be in contact with the surface. As an example, food on these surfaces may become contaminated leading to spoilage, reduced shelf life for food, or, in some cases, food poisoning.
In addition to these obvious problems, microbes growing in a cleaning product must be eating something and that “something” is almost certainly the organic materials such as surfactants, chelants, hydrotropes, polymers, solvents, etc. which were intentionally added to the product. If the microbes eat these materials, then the materials are not available to function as intended. This leads to loss of cleaning ability, loss of formulation homogeneity, loss of formulation viscosity, the creation of off-odors, and/or bulging containers due to off-gassing. The byproducts of microbial metabolic activity may alter the solution pH leading to the problems listed, even if there is some other food source the microbes are consuming. Furthermore, these byproducts may themselves be toxic to humans and animals.
Given these potential problems, microbial contamination of cleaning products is something which must be avoided.
The question may be asked, can we make cleaning products which are free of microbes? Unfortunately, microbes are found everywhere, including in the synthetic and natural materials which are used to make many of the components of cleaning products. So, if we cannot make cleaning products which are free of microbes, we must include something in the cleaning product to protect the desirable components from the microbes which are present. That something is commonly referred to as a “preservative”.
Preservatives generally function by preventing the growth of microbes. These materials may not directly kill the microbes the way that a disinfectant or sanitizer does, regardless the microbes do not grow and reproduce. Preservatives, therefore, keep the cleaning product essentially free of microbes. It must be stressed, that preservatives are not disinfectants or sanitizers which are products designed to kill microbes on surfaces. Preservatives are designed only to prevent microbial growth in the undiluted cleaning product. As soon as a concentrated cleaning product is diluted to use strength, the preservative efficacy is reduced to essentially zero and any microbes present are free to start growing. This is why diluted cleaning products must be used or discarded generally within 24 hours of being diluted.
No single preservative will work against all microbes in all product types. The pH of the solution is one of the biggest factors to be considered when selecting the preferred preservative. For example, organic acids such as lactic acid are very efficient preservatives in solutions with pH below the acid’s pKa value. At pH greater than the pKa value the acid is largely deprotonated and completely ineffective as a preservative.
Figure 1 shows the pH range at which various types of microorganisms can live. It should be noted that microorganisms can become acclimated to the environment in a chemical plant and these organisms can survive in even broader pH ranges, perhaps by 0.5 to as much as 1.5 pH units higher and lower than non-acclimated organisms. Figure 1 also shows the typical pH of many cleaning products. Not surprisingly this shows that many cleaning products have a pH suitable for microbial growth.
Figure 1: pH necessary for microbe survival and common cleaning product pH values
Table 1 shows the pH range at which the common preservative materials are microbiologically active and the types of microorganisms they are active against.
Table 1: Effective pH range for common preservatives
preservative | effective against | pH range for efficacy |
methylparaben / propylparaben | bacteria / fungi | 3 – 8 |
glutaraldehyde | bacteria / fungi | 3 – 9 |
IPBC (iodopropynylbutylcarbamate) | fungi | 4 – 10 |
CTAC (chloroallyl-triaza azoniaadamantane chloride) | bacteria | 2 – 12 |
DMDMH (dimethylol dimethyl hydantoin) | bacteria | 3 – 10 |
DMO (dimethyl oxazolidine) | bacteria | 7 – 11 |
BIT (benzoisothiazolinone) | bacteria | 2 – 12 |
CMIT / MIT (chloromethylisothiazolinone / methylisothiazolinone) | bacteria / fungi | 2 – 8 |
MIT (methylisothiazoline) | bacteria | 2 – 12 |
OIT (octylisothiazolinone) | fungi | 2 – 10 |
BNPD (bromonitropropane-1,3 diol) | bacteria | 3 – 9 |
To be approved for use as a preservative in cleaning products, a material must be registered with the US EPA (or with the corresponding regulatory authority in the country where it will be used). The EPA sets strict performance requirements and limits on the concentration of preservatives in cleaning products to ensure that the preservative is effective and does not constitute an unnecessary hazard to potential users of the cleaning product. The EPA process for approving preservatives is extensive and highly resource (both human and fiscal) exhaustive. The process includes data generation at the manufacturer, data submission from the manufacturer to EPA, data review by EPA, and the EPA final decision. All EPA-approved preservatives are re-assessed every 15-years.