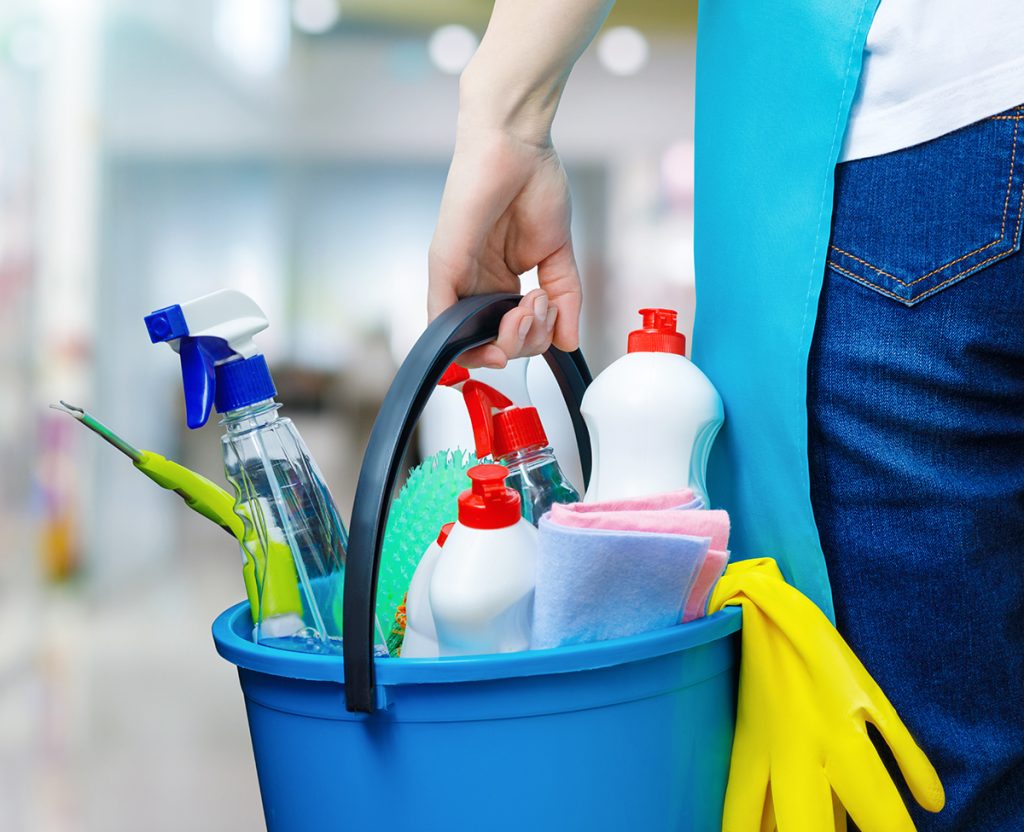
Microbial contamination of cleaning products is highly undesirable for several reasons. Primary among these is the fact that we clean to remove contaminants from surfaces, and if the cleaning solution is microbially contaminated, we are, in fact, contaminating the surface rather than removing contaminants from the surface. This means that the surface is not clean, regardless of its physical appearance, and this can lead to contamination of materials that may be in contact with the surface. As an example, food on these surfaces may become contaminated leading to spoilage, reduced shelf life for food, or, in some cases, food poisoning.
In addition to these obvious problems, microbes growing in a cleaning product must be eating something and that “something” is almost certainly the organic materials such as surfactants, chelants, hydrotropes, polymers, solvents, etc. which were intentionally added to the product. If the microbes eat these materials, then the materials are not available to function as intended. This leads to loss of cleaning ability, loss of formulation homogeneity, loss of formulation viscosity, the creation of off-odors, and/or bulging containers due to off-gassing. The byproducts of microbial metabolic activity may alter the solution pH leading to the problems listed, even if there is some other food source the microbes are consuming. Furthermore, these byproducts may themselves be toxic to humans and animals.
Given these potential problems, microbial contamination of cleaning products is something which must be avoided.
The question may be asked, can we make cleaning products which are free of microbes? Unfortunately, microbes are found everywhere, including in the synthetic and natural materials which are used to make many of the components of cleaning products. So, if we cannot make cleaning products which are free of microbes, we must include something in the cleaning product to protect the desirable components from the microbes which are present. That something is commonly referred to as a “preservative”.
Preservatives generally function by preventing the growth of microbes. These materials may not directly kill the microbes the way that a disinfectant or sanitizer does, regardless the microbes do not grow and reproduce. Preservatives, therefore, keep the cleaning product essentially free of microbes. It must be stressed, that preservatives are not disinfectants or sanitizers which are products designed to kill microbes on surfaces. Preservatives are designed only to prevent microbial growth in the undiluted cleaning product. As soon as a concentrated cleaning product is diluted to use strength, the preservative efficacy is reduced to essentially zero and any microbes present are free to start growing. This is why diluted cleaning products must be used or discarded generally within 24 hours of being diluted.
No single preservative will work against all microbes in all product types. The pH of the solution is one of the biggest factors to be considered when selecting the preferred preservative. For example, organic acids such as lactic acid are very efficient preservatives in solutions with pH below the acid’s pKa value. At pH greater than the pKa value the acid is largely deprotonated and completely ineffective as a preservative.
Figure 1 shows the pH range at which various types of microorganisms can live. It should be noted that microorganisms can become acclimated to the environment in a chemical plant and these organisms can survive in even broader pH ranges, perhaps by 0.5 to as much as 1.5 pH units higher and lower than non-acclimated organisms. Figure 1 also shows the typical pH of many cleaning products. Not surprisingly this shows that many cleaning products have a pH suitable for microbial growth.
Figure 1: pH necessary for microbe survival and common cleaning product pH values
Table 1 shows the pH range at which the common preservative materials are microbiologically active and the types of microorganisms they are active against.
Table 1: Effective pH range for common preservatives
preservative | effective against | pH range for efficacy |
methylparaben / propylparaben | bacteria / fungi | 3 – 8 |
glutaraldehyde | bacteria / fungi | 3 – 9 |
IPBC (iodopropynylbutylcarbamate) | fungi | 4 – 10 |
CTAC (chloroallyl-triaza azoniaadamantane chloride) | bacteria | 2 – 12 |
DMDMH (dimethylol dimethyl hydantoin) | bacteria | 3 – 10 |
DMO (dimethyl oxazolidine) | bacteria | 7 – 11 |
BIT (benzoisothiazolinone) | bacteria | 2 – 12 |
CMIT / MIT (chloromethylisothiazolinone / methylisothiazolinone) | bacteria / fungi | 2 – 8 |
MIT (methylisothiazoline) | bacteria | 2 – 12 |
OIT (octylisothiazolinone) | fungi | 2 – 10 |
BNPD (bromonitropropane-1,3 diol) | bacteria | 3 – 9 |
To be approved for use as a preservative in cleaning products, a material must be registered with the US EPA (or with the corresponding regulatory authority in the country where it will be used). The EPA sets strict performance requirements and limits on the concentration of preservatives in cleaning products to ensure that the preservative is effective and does not constitute an unnecessary hazard to potential users of the cleaning product. The EPA process for approving preservatives is extensive and highly resource (both human and fiscal) exhaustive. The process includes data generation at the manufacturer, data submission from the manufacturer to EPA, data review by EPA, and the EPA final decision. All EPA-approved preservatives are re-assessed every 15-years.